It happens infrequently to be able to witness the making of a statue, especially one that is of considerable size – a height of 172 cm and a weight of 90 kg- as in the case of the Summer.
It happened a few weeks ago that we had to do this work, and it had been a while since we had held this particular form in our hands again: so it was almost natural for us to think of filming the execution, because the whole process, from the moment of handling the imposing plaster form, is rare to see and really interesting.
There were long moments of filming, because clay does not care for the “television” times – or rather the very short “reels” we have to submit to today. So we tried to capture the highlights of the creation, so that you could learn about the difficult stages of production and see what it means to make such an object by hand; In the end, a small series was created, which will also be published on our social channels, so that you can witness the creative spectacle that leads to the completion of a work that is more unique than rare. This creative process is the result of centuries of traditional craftsmanship, which is handed down only and only within the historic kilns of Impruneta.
Summer is one of the famous Four Seasons, there are in fact 3 other allegorical statues that are part of a collection – Spring, Autumn, Winter, whose models were recovered from the archives of the historic Sannini Furnace in Impruneta, in business until the early 2000s.
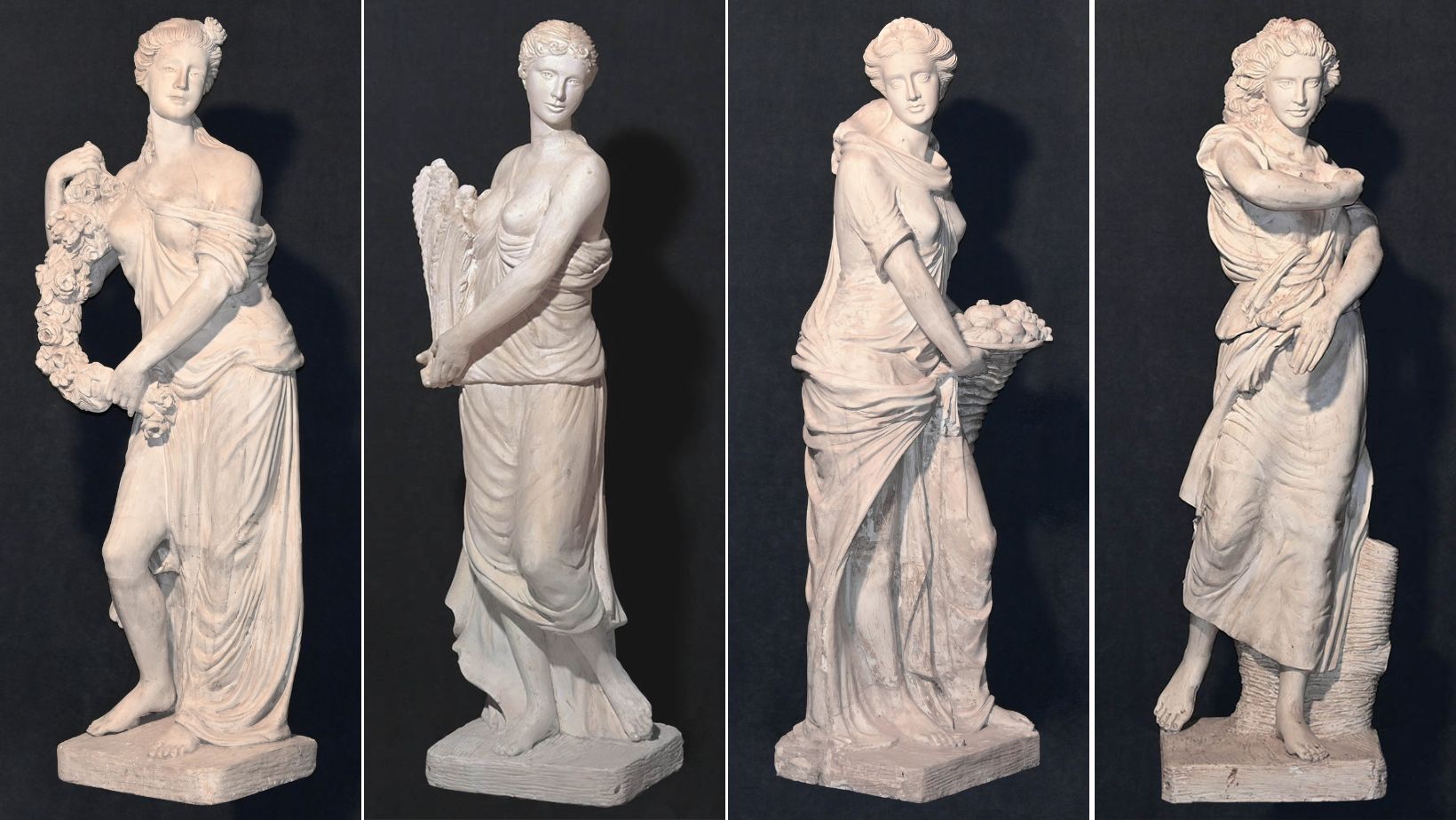
The work begins with the transport of the plaster mold, which, due to its size and weight, is taken from the mold room by a forklift and brought to the artisans, who, with patience and devotion, begin to cast the statue piece by piece. One trip is not enough, at least three are needed!
Once the artisans have received all the pieces of the plaster mold, they have to recreate the “puzzle” – if you can call it that – of the cast itself: this mold is actually made up of 6 separate molds that form the larger parts of the figure – legs, torso, arms, chest and face – but inside them are a series of smaller pieces (called dowels) that serve to define the miniaturized details of this beautiful statue.
Since this is an item that is not handled every day, this step also requires time and attention;
Then you can start with the liming. The creation of a statue may seem simple when you admire the final result, but in reality there are many steps and a great deal of experience is needed to complete such a work; moreover, it is not enough for one craftsman to chisel the clay, in this case two work together: first of all to pass on the art to the younger generations (in fact, there are no schools where the art of terracotta is taught), and then to make sure that each piece is ready with its complement, so that everything dries evenly.
Sounds easy – especially when you see master craftsmen working with a smile!
The first part to be created is the base, which will support the entire statue and carry all of its weight; For this reason, supports will be built inside it, also made of clay, which will help the statue to be stable and durable over time and, at this stage, when the clay is still fresh, will prevent it from collapsing on itself. This part will probably never be seen by anyone, but the care and precision with which the hands of the master craftsmen work is still the same: the lattice of supports hidden in the floor is “only” a functional part, but it still looks poetic to us…. Now this part of the statue will rest in the mold to allow the clay to dry and harden.
The next step is to cast the torso and face of Summer, who, since Greek and Roman mythology, has been represented by the appearance of a beautiful young woman: the goddess Demeter (Ceres to the ancient Greeks), who was chosen as the symbol of the warm season characterized by “harvests” and who, with her benevolent gaze, promises prosperity.
The whitewashing is not finished yet, the arms, the hands and the symbol of summer, the bundle of wheat, are still missing. Each time the procedure is the same: a layer of clay is applied and pressed against the plaster mold, then, to check that the thickness is even, a finger is inserted into the clay up to the first phalanx, and from there it is adjusted, adding more or removing the excess. Before closing the mold, we smooth the inside, then we scratch the contours of the clay with the prongs of a fork and apply the famous “borbottina” (a liquid mixture of water and soil that acts as a glue and creates bubbles that pop when mixed, in Tuscan we say “borbottare” – “to mumble”).
We finished liming each part of the statue that represents summer. We let time pass so that the clay could rest and dry in the mold and take on the proper features. Opening the plaster molds is just amazing – it is the exact moment when we can see the result of our work for the first time, and it is always a thrill! But air is electric, because we have to be very careful to remove even the smallest piece of plaster without risking to ruin the details of Summer’s beautiful face. At the end of this stage, we have to cover the “unmolded” parts well so that they do not dry out too much while we wait for the rest of the statue to be finished.
Those who work in the kiln are often asked why there are long production times. Some products can take up to 90 days to complete. An example of this is Summer; for such a large statue, one must have the patience to wait for the clay to take its time: for example, when the lower part needs to be removed from the mold, it requires the use of some wooden supports so that the statue does not collapse on itself and is ready to dry evenly and stably. Until now, the base has been in the plaster mold, but from now on it will have to contend with gravity and the weight of all the parts that will be added in the next steps.
You cannot be in a hurry if you want something beautiful and durable….
It has been weeks since we poured the first handful of clay into the shape of the Summer statue. Now it is time to put all the pieces together. Michele, the artisan who does most of the work on these statues, is very excited and coordinates the work of his colleagues, Lorenzo and Alessio, because each step has to be done with the utmost precision. After a few moments of suspense, one is left breathless to admire the still raw beauty of this magnificent work.
Often, watching the artisans at work, one has the feeling of stepping back in time to the Renaissance, when great artists put their hands to works that are still true myths for us today…
We have come to the last act, it seems as if we are watching a diva in make-up before a performance. …. The statue is now recognizable and only needs to be finished. Each detail, even the smallest, is defined by hand with the typical tools of the terracotta craft: small wooden sticks, water and brushes, but the grace and delicacy with which the masters skim the surface make it seem as if it could come to life at any moment.
The “trick“, if we may say so, is to give each piece the right amount of attention and time….
And now, to continue the theatrical metaphor, we are almost ready to go on stage!
Here is the Summer statue, so beautiful and imposing that we could spend hours admiring it…. Now it is time for it to rest; it needs to dry slowly so that the clay will gain strength and keep its shape over time.
Before we can see it finished and ready for its final destination, along with the other 3 of the 4 seasons
we will have to wait another month or so; during this time, the Summer Goddess must first dry out in the open air so that the water contained in the clay can slowly evaporate without risking breaking the beautiful form it has taken. Gradually – and always without haste – the statue is transferred to the “drying room”, a room with a controlled temperature of about 60°C, where it remains for as long as necessary to continue the drying process, slow and progressive, again to prevent the clay, which shrinks too quickly, from causing cracks in the work.
Finally, the statue is fired in an oven at about 1000°C. After about 72 hours, the statue is taken out of the oven and allowed to cool to room temperature. We are now at the final step: wetting. After firing, each terracotta is taken outdoors and moistened several times; this is done in order to restore the water lost during firing and to stabilize the product, which will thus last for a very long time.
It has been almost two months since this work began, but we believe we can say that the wait will be richly rewarded…
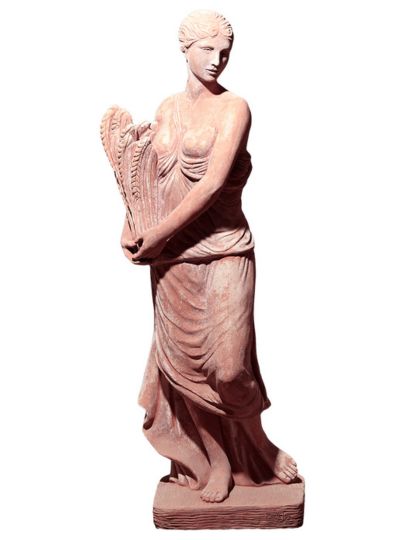
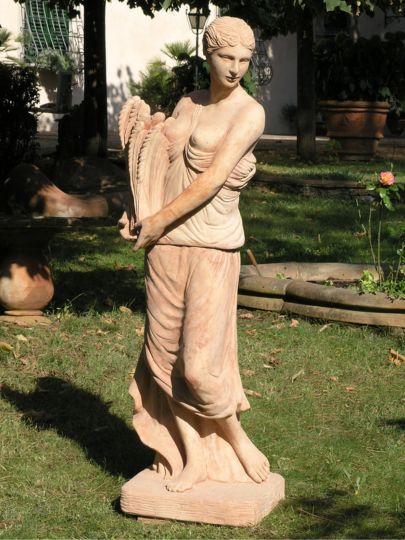
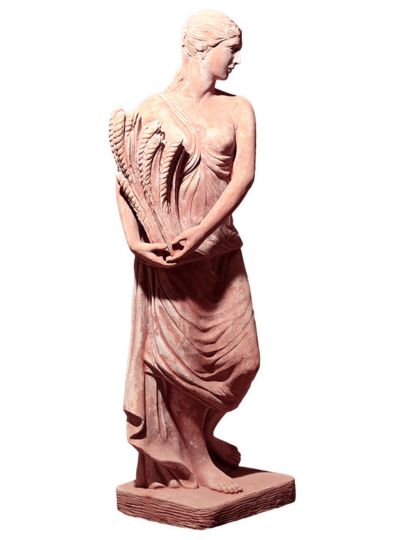