Some time ago, we showed you the entire process of creating one of the quintessential classical statues: the Allegory of Summer.
This time, we would like to take you on a journey that will lead you to the TOP MODEL, the modern answer to those who are looking for a terracotta statue – whether for outdoor or indoor use – with an undeniable aesthetic impact, without any hint of classicism.
In this video you can see the whole process of creating super-modern top model statue.
When Poggi Ugo decided to expand its collection to include items with a contemporary and minimalist taste, it needed a statue that could also be used in eclectic and cosmopolitan environments.
The story of this creation is not only about the production of a terracotta accessory, but also about one of our oldest craftsmen – Mauro – who, on the eve of his retirement – after 42 years of an honourable career spent exclusively at Poggi Ugo terrecotte – teaches the art to a very young and passionate apprentice.
This is another peculiar aspect of working in terracotta: There are no schools to learn the craft, the only way to learn the art of the kiln is to do it yourself.
Duccio has been a student of Mauro’s for some time now, and in the last days of his master’s work he tries to remember every single gesture shown to him, every little secret revealed to him.
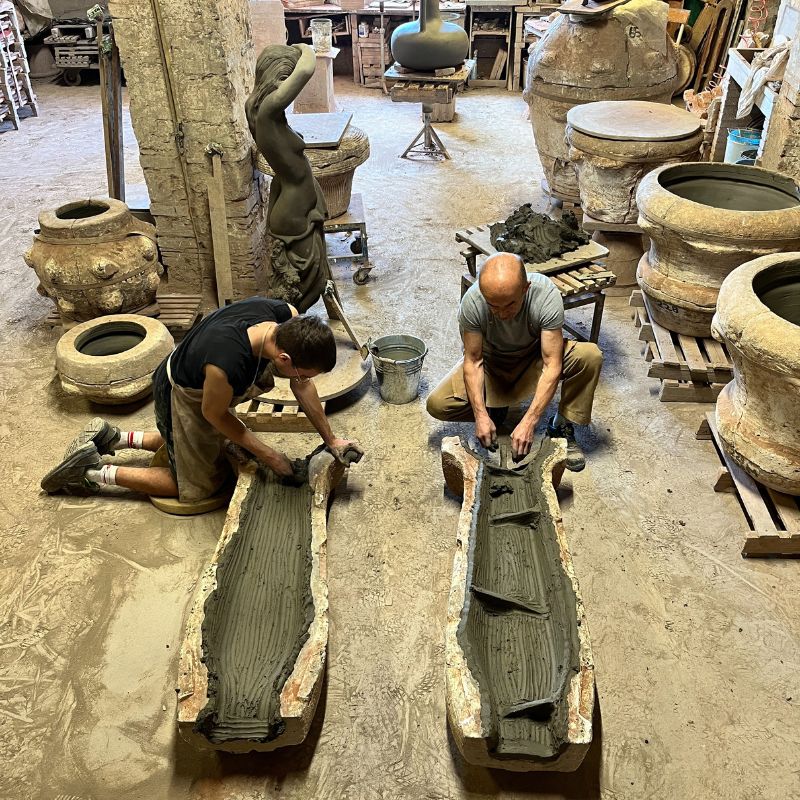
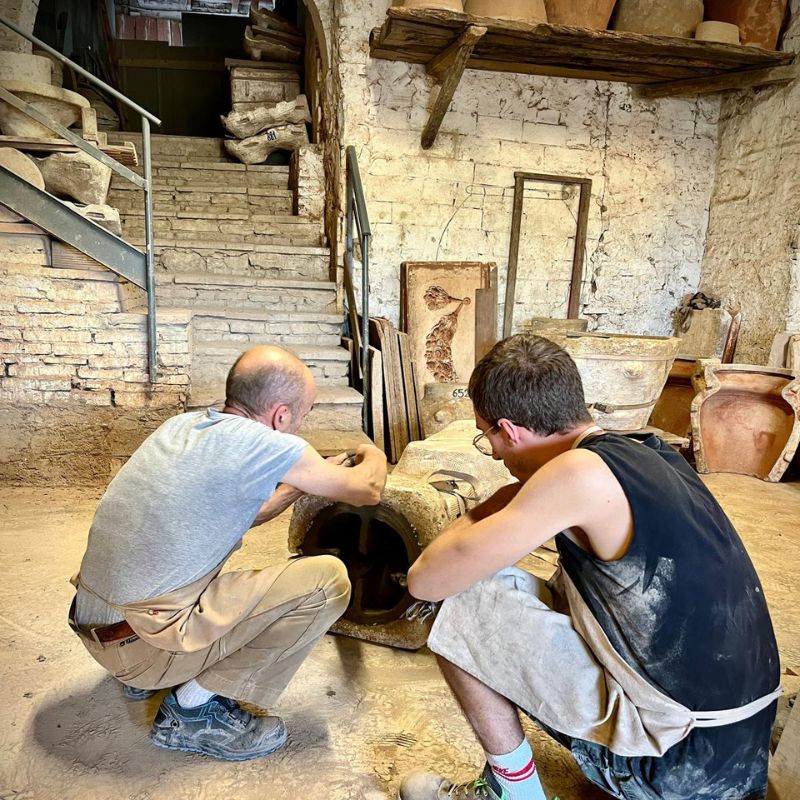
Moments of “schooling” in the kiln: this is how young people learn the art of terracotta, watching and listening to their more experienced colleagues who patiently pass on the techniques and secrets that each piece brings.
Once again, the starting point is a plaster mould.
There are four moulds in total and the craftsman begins his work with care and patience from the bottom of the statue;
Those who are familiar with the work of terracotta know that it takes a great deal of serenity to see the completion of a work made by hand: The processes are long and dictated by the clay time, not man’s.
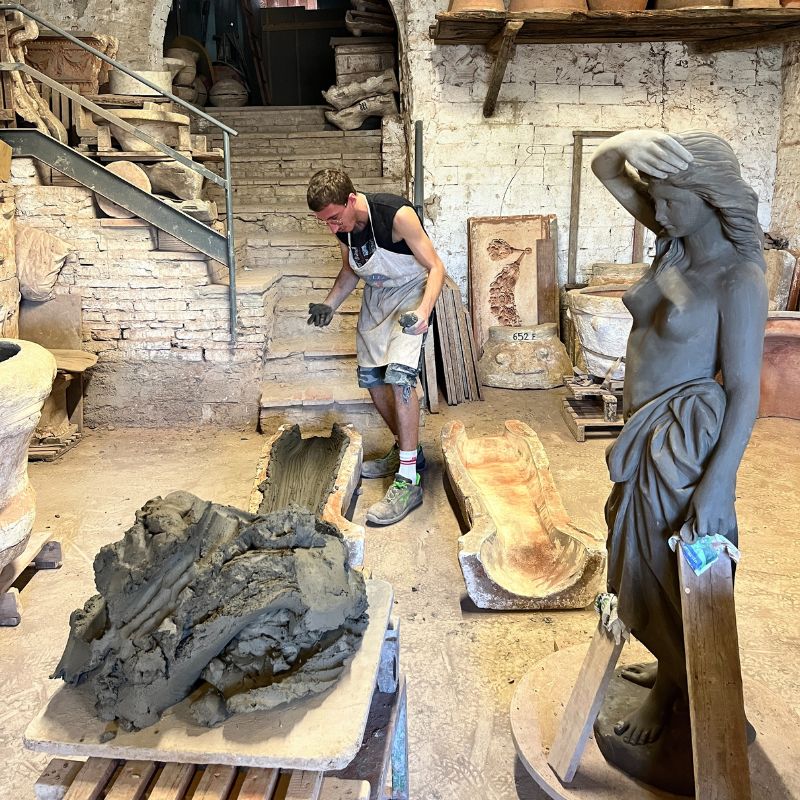
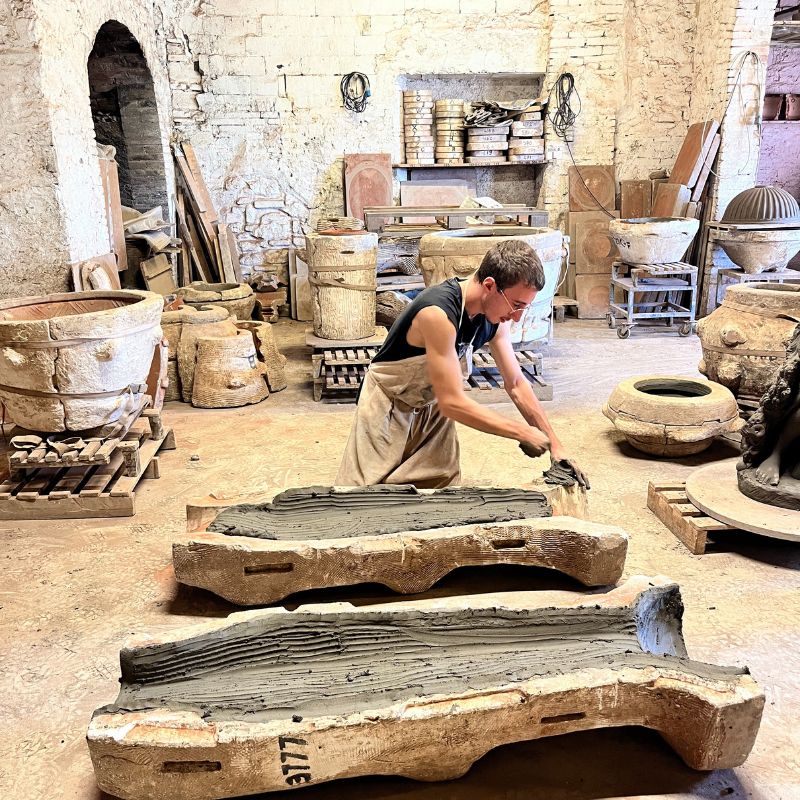
The cast of the lower part of the statue.
Also in the case of the Top Model cast, one must be very careful about the thickness, which must be homogeneous everywhere, then one must be careful to line the clay well with one’s fingers to burst the air that remains trapped between its particles, so as to have a perfect and long-lasting result.
The work in the kiln may seem repetitive because it is based on tried and tested craft techniques that have been reproduced here in Impruneta for hundreds of years; however, this does not tire us, on the contrary, it allows us to acquire the necessary competence to measure ourselves with unprecedented articles, with forms that have never been produced and experimented with before, as in the case of this statue.
>Once the liming of the two lower parts is complete, the mould can be laid down and closed tightly with straps to allow it to lie flat for the time needed for the clay to dry slowly.
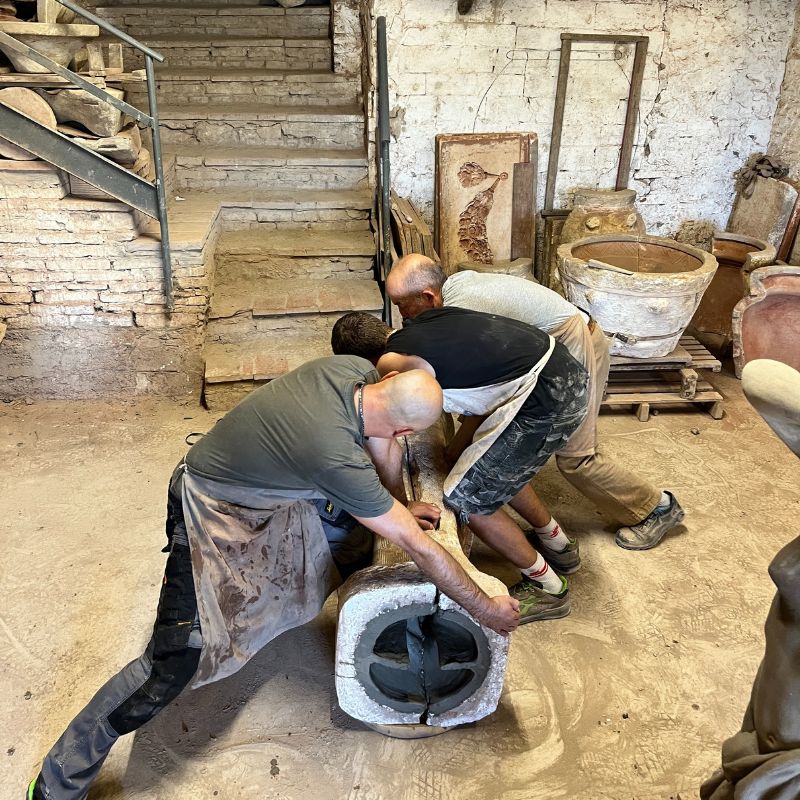
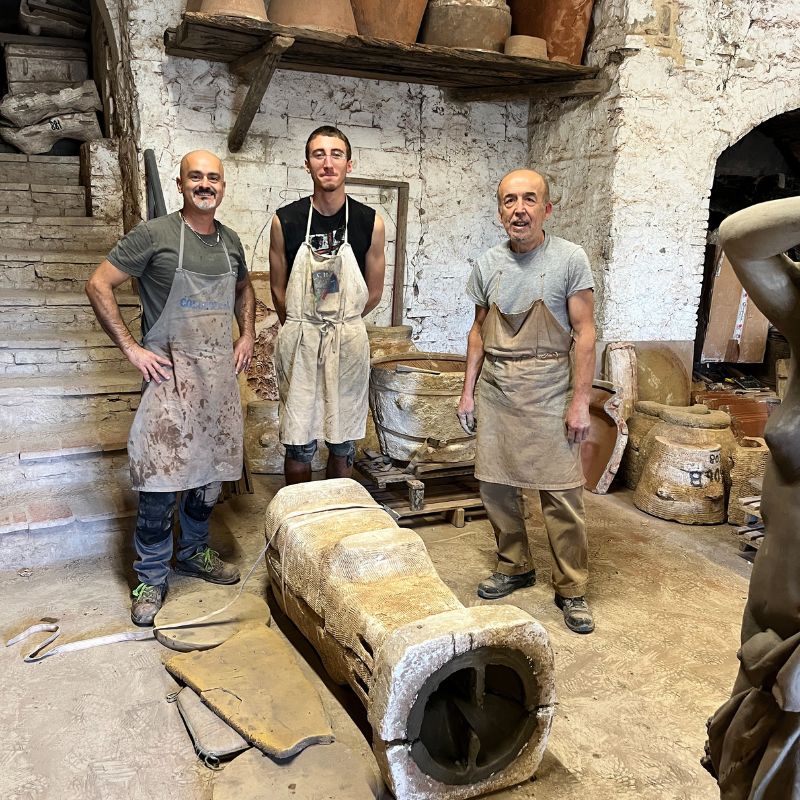
The two lower parts of the plaster cast are joined together and tied with straps so that the base of the upper model can take shape.
Meanwhile, the upper part of the statue is being worked on.
The plaster casting technique was continued. The upper part is also made up of two parts, which are joined together after the plaster cast has been made using the now familiar ‘borbottina‘ (a fairly liquid mixture of clay and water that acts as an adhesive).
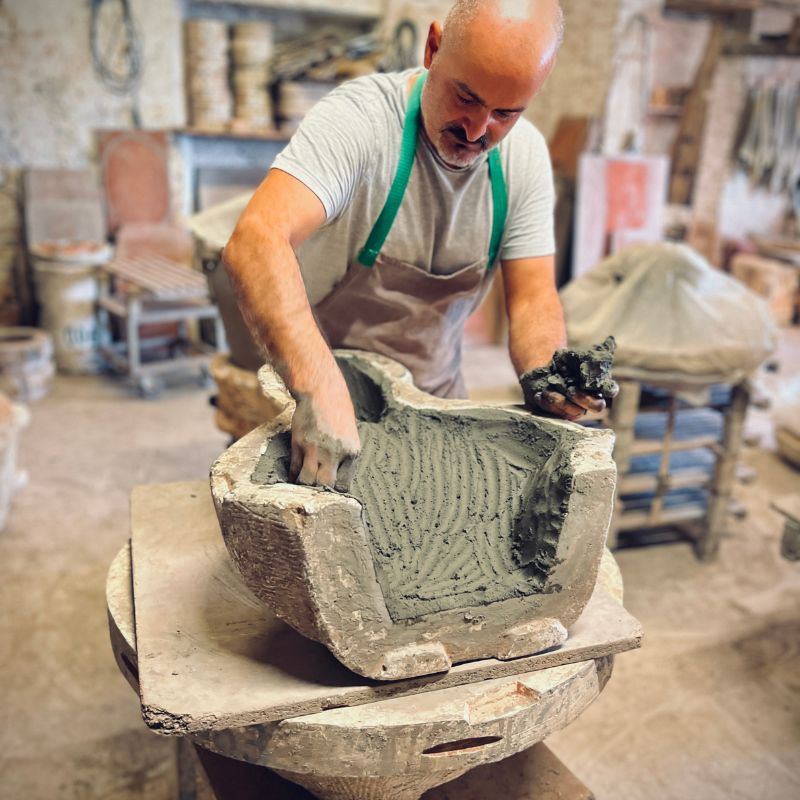
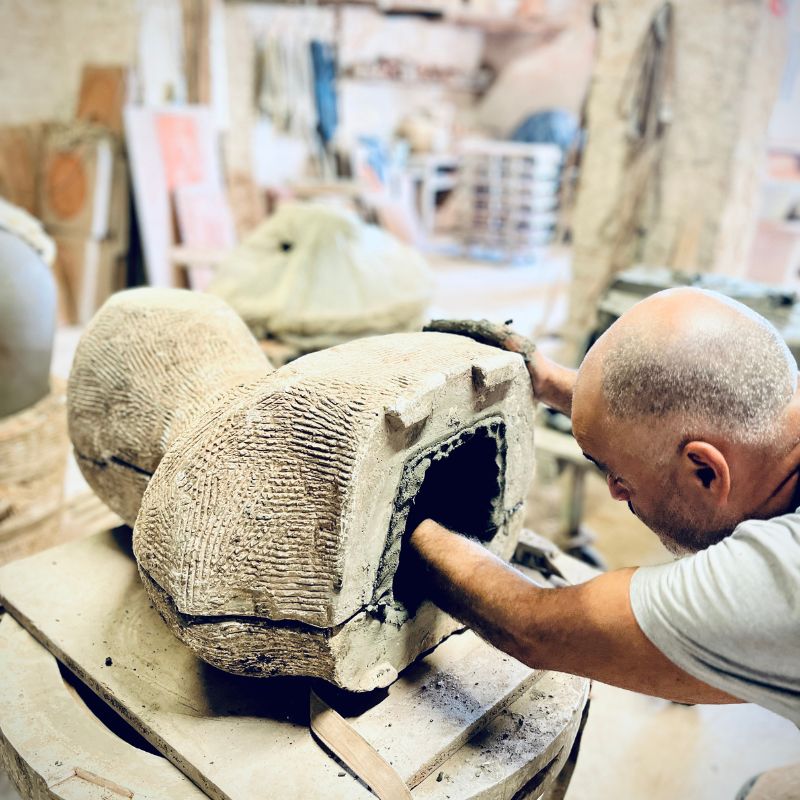
After casting the two upper parts of the statue, the craftsman joins them together using the now-familiar ‘mumbler’.
Now comes the waiting… We wait at least a week, the time it takes for the clay to dry a little and take its new shape. Until we feel that the earth is dry enough to bear the weight of gravity without the support of plaster, we cannot decide to remove it, but now the time has come…
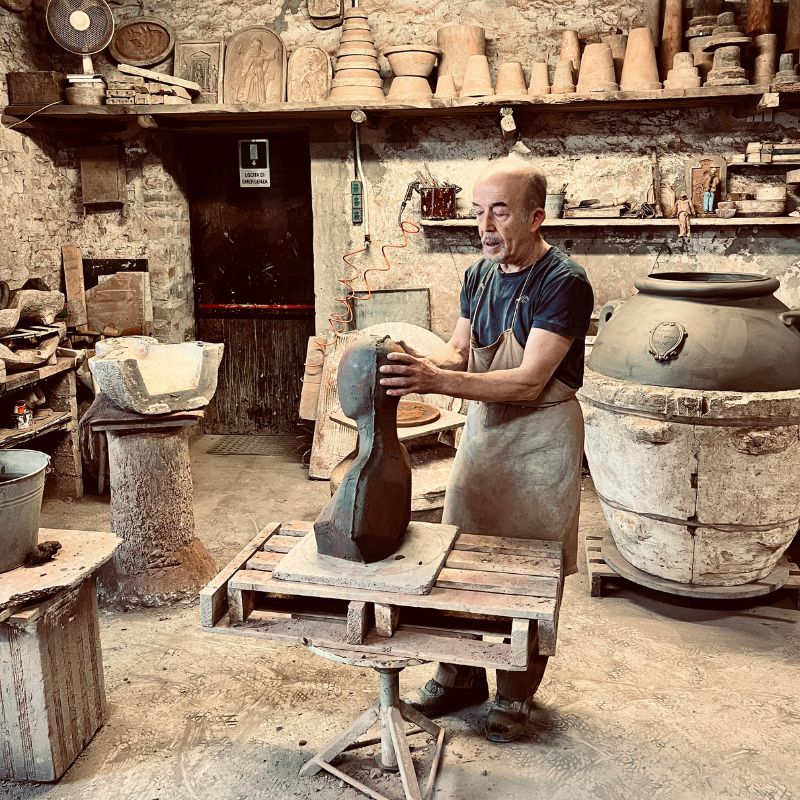
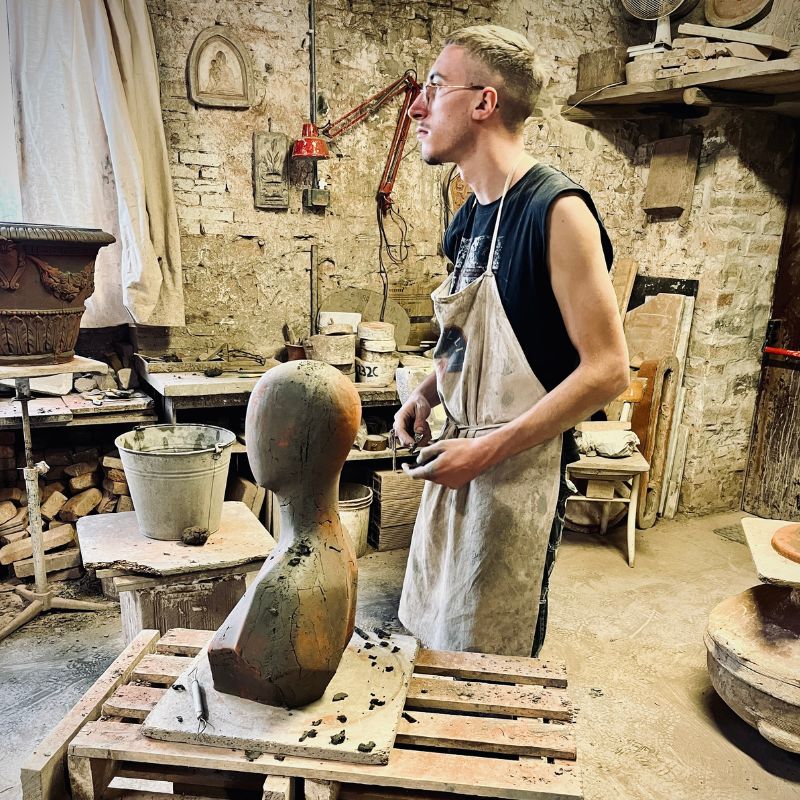
We unmould the top part of the top model and then finish it.
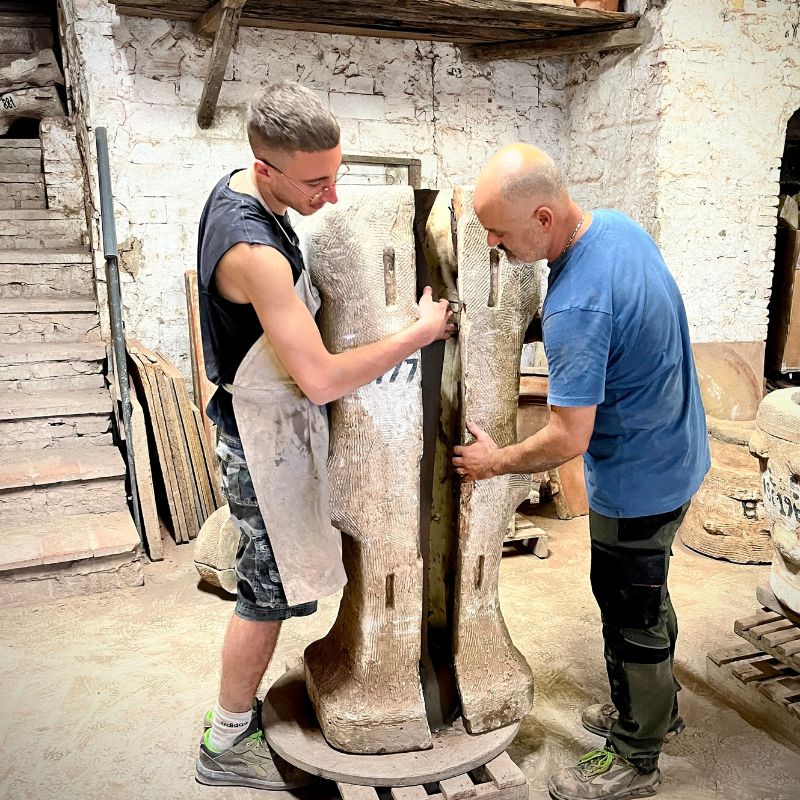
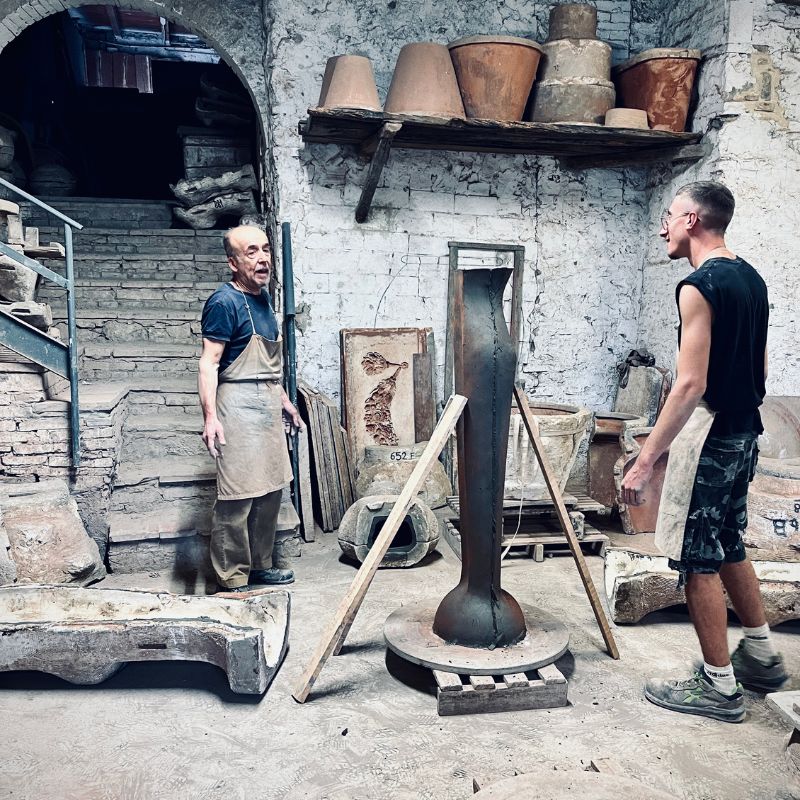
The unmoulding of the bottom part of the Top Model.
The statue must now be cleaned: this is done with simple tools such as gouges, scrapers and brushes; the surface of the statue must be perfect, impeccable, without even the slightest defect, which is why an almost maniacal eye and attention are needed to complete this phase; the same gestures are made for the lower part – the legs – as for the upper part, which represents the bust of the Top Model.
Once the finishing touches have been made, it is time for the final composition, when the two parts are joined together and the 176 cm of pure beauty of this statue can be admired for the first time.
Mauro and the other artisans know that the perfect combination of bust and body requires patience and small gestures, attention and millimetric care, because a Top Model cannot be flawed.
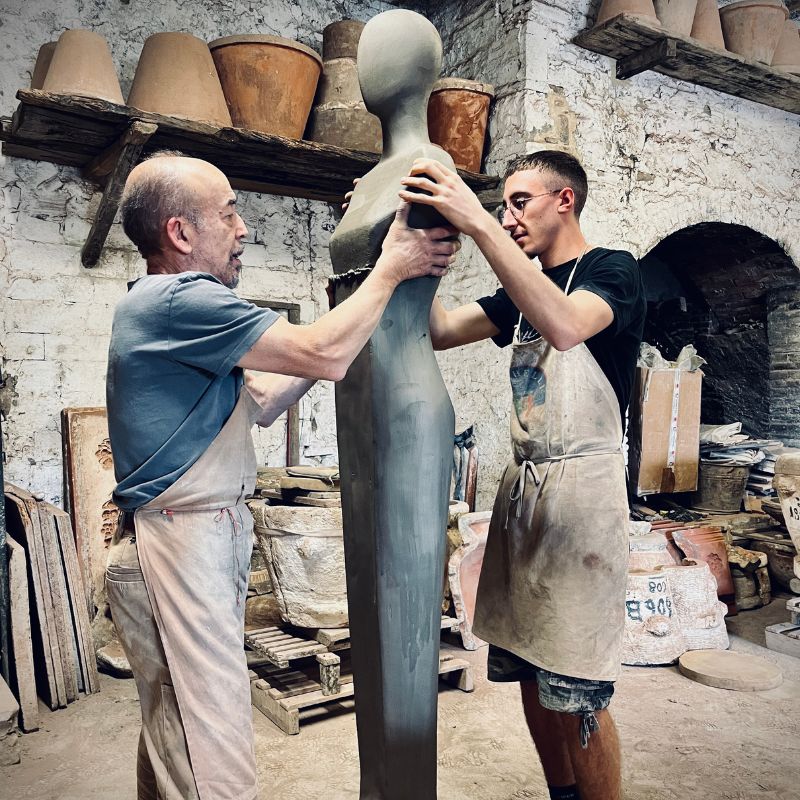
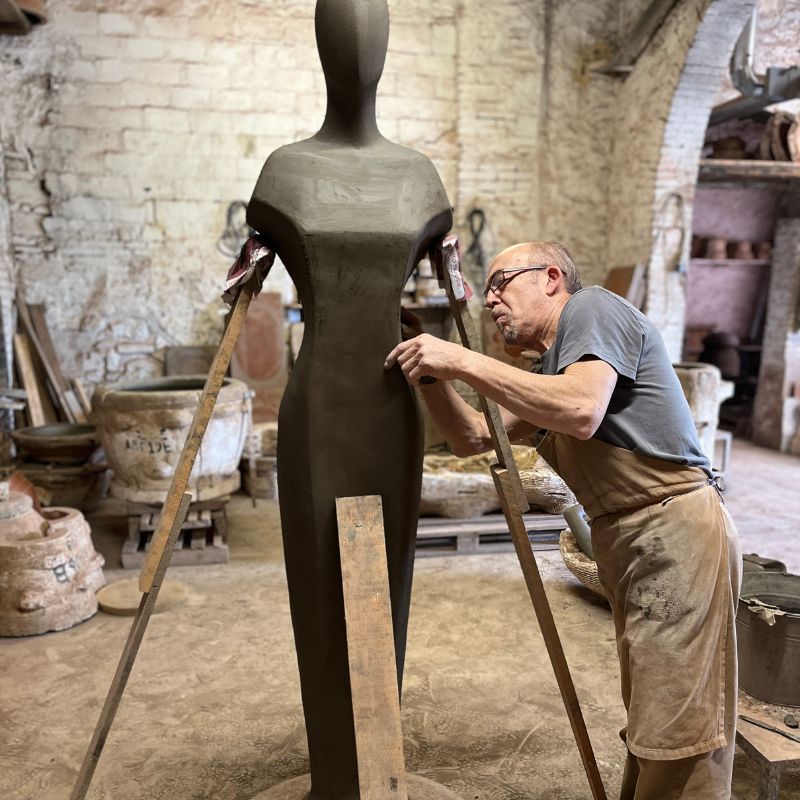
We join the two parts of the statue and finally admire the Top Model in its entirety.
Once even the smallest seam mark has been removed, the Top Model must be left to rest – which, for clay, means drying slowly in several stages:
at room temperature, motionless for days, the exact number varies depending on the season, now in autumn it takes at least ten, after which the statue will be moved to a temperature-controlled room (the drying room at around 60°C) where it will remain for a couple of more weeks, before being fired in the kiln in which it will do 4 days of firing at 1000°C and then 5 days of cooling in a closed kiln.
It is very important that each step involving a change in temperature is done slowly and gradually to allow the clay to harden.
The statue has finally taken on the colour of terracotta, with the delicate powdery notes typical of the Poggi Ugo clays of Impruneta.
Now our men carefully carry it to the forecourt in front of the kiln where it is thoroughly moistened (this is the last and very important step in the process) to restore the water lost during the firing; this operation stabilises the terracotta forever and ensures the eternal beauty of our Top Model.
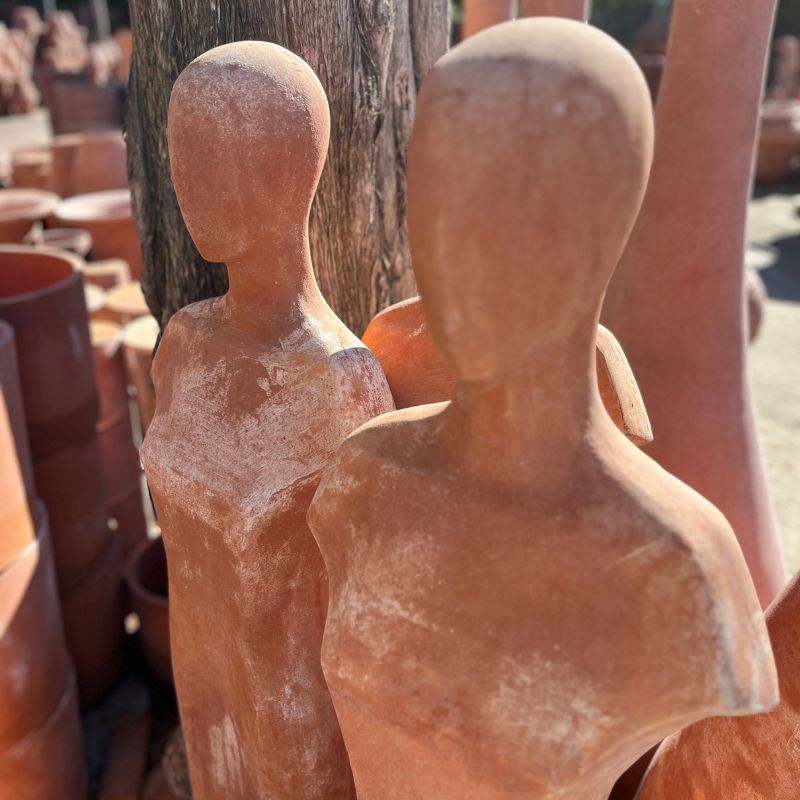
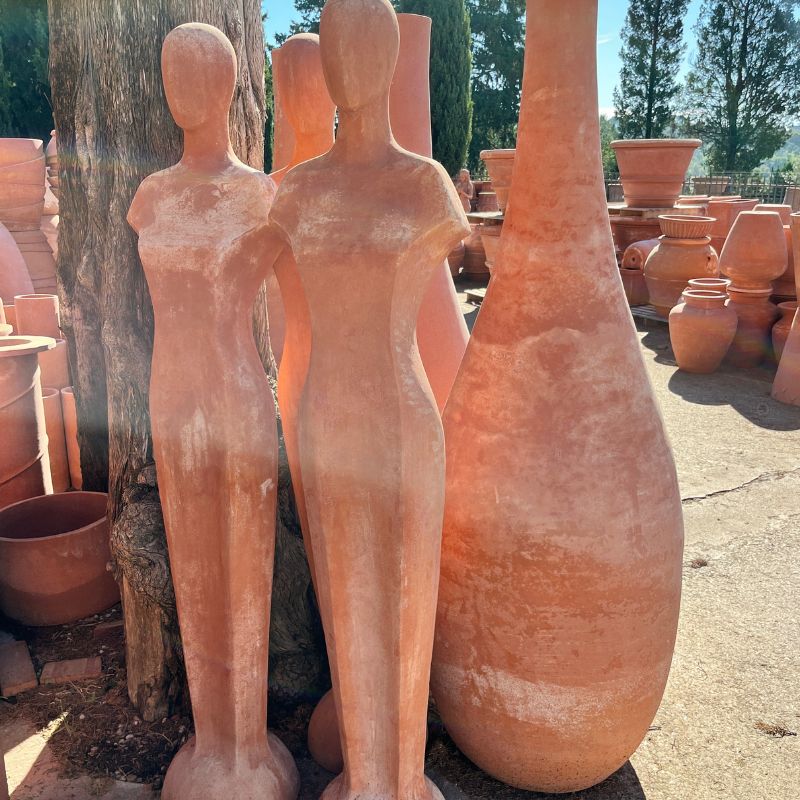
Finally, the Top Model is ready an we admire her in all her perfect beauty.
Stripped of all decorative and opulent frills, the TOP MODEL is characterised by sculpted and well-defined lines, reminiscent of the great models of the fashion world: 176 cm tall, she is proud, has no eyes, but her gaze tends towards infinity.
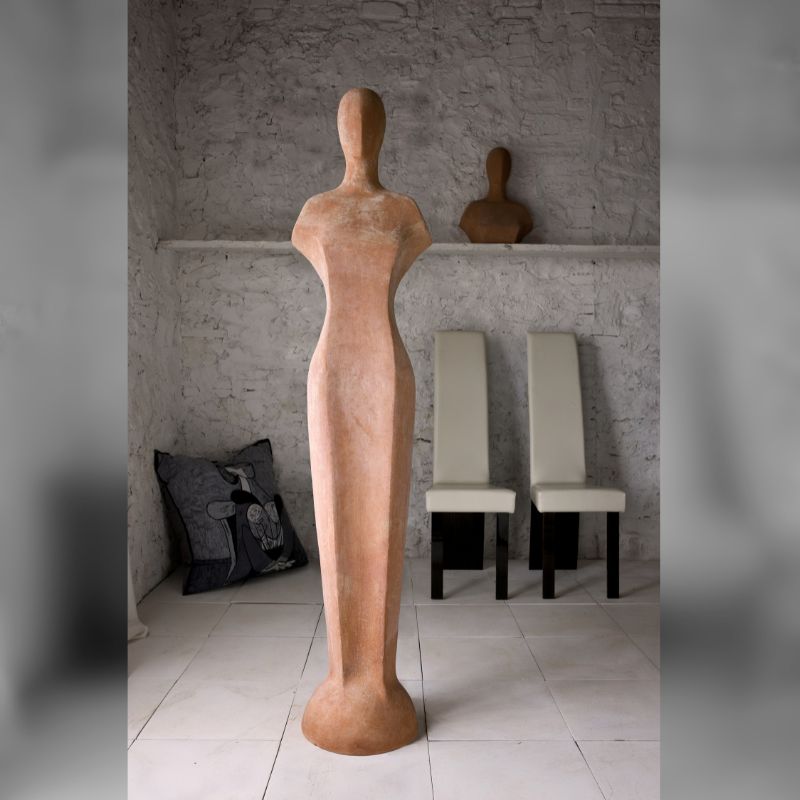
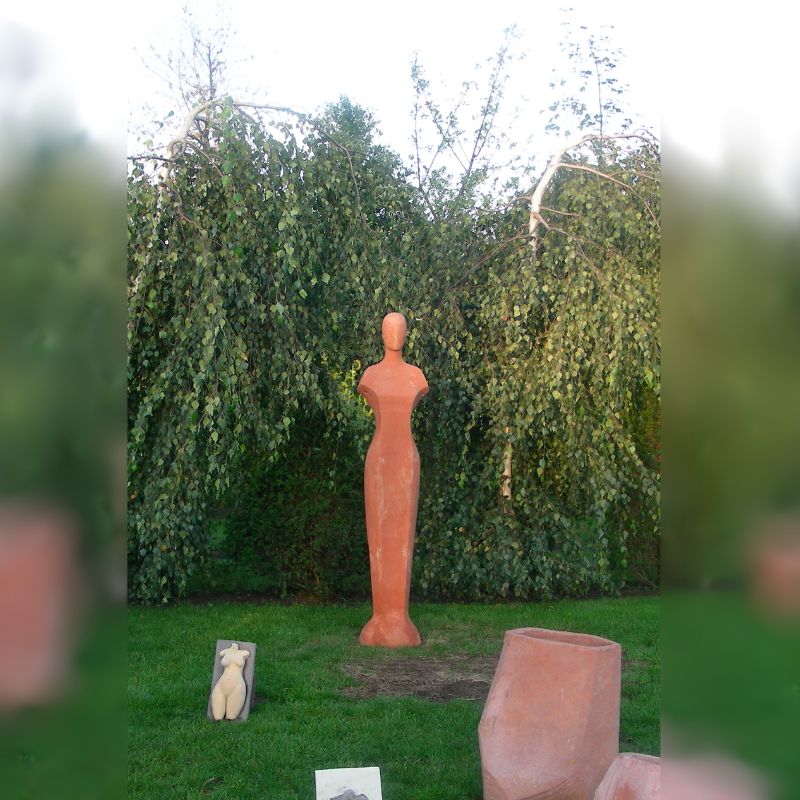
The Top Model, like most of Poggi Ugo’s terracotta articles, is also produced in the GrigioLava variant and a version of the bust only is also available, perfect to be presented alone or on top of a column, such as the essential ‘Wall Column’.
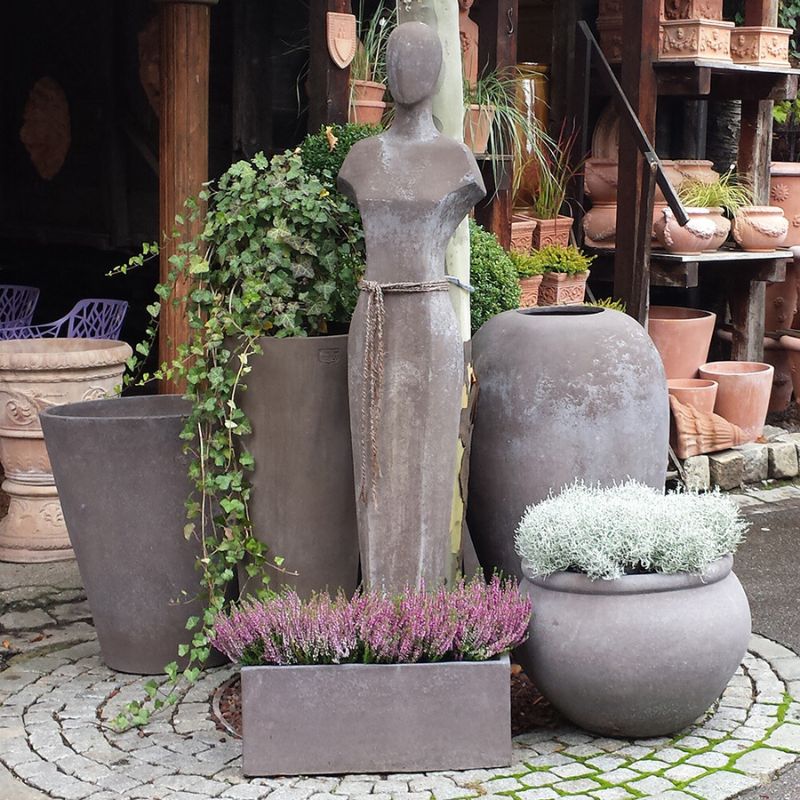
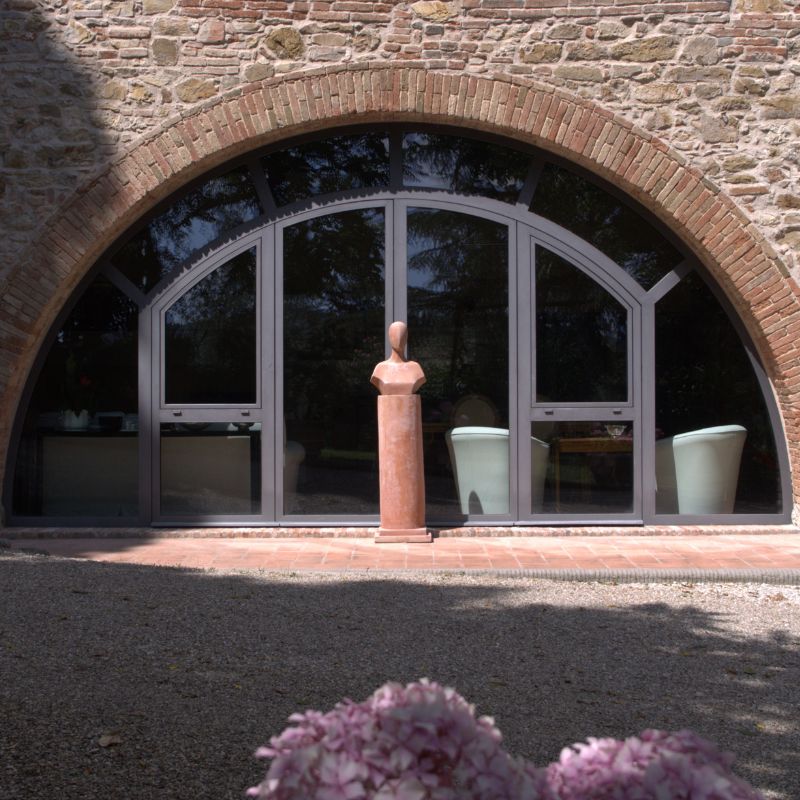
This imposing craftwork, with its austere and solemn beauty, is the current answer to those who are looking for a statue – both indoors and outdoors – of unquestionable aesthetic impact, stripped of all opulence; it can be used to enhance the area around a swimming pool, to embellish the entrance or lobby of a hotel, or to transform the hall of a restaurant.
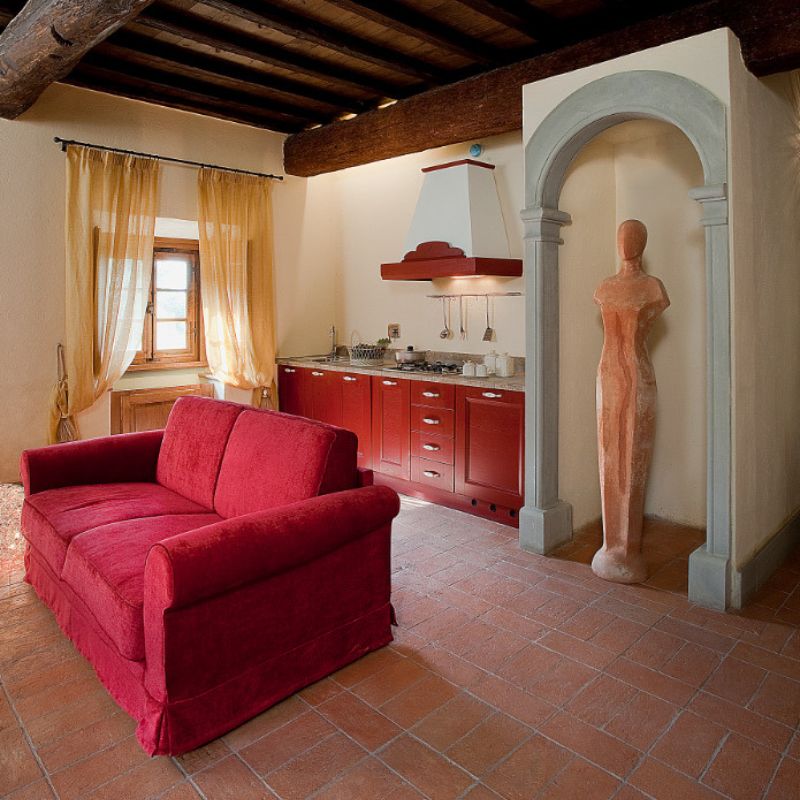
As you have seen throughout this journey of creation, the Top Model’s geometric and clear lines are shaped by the skilled hands of our master craftsmen, who take the time to cast, shape, finish, pay attention to every last detail and then wait.
They wait for this simple mixture of clay and water to turn into something exhilarating.